Making a printed circuit board with a CNC machine
In this part of the articles of Arya Madar Arjomand, we will introduce various methods of making printed circuit boards.
There are several ways to make a printed circuit board or PCB, and you should choose one of them based on the complexity of the desired printed circuit and the facilities you have. Most of these methods are different in creating designs on fibers, but they can be divided into the following main methods.
Building a circuit with Letrast
Making a printed circuit with anti-acid ink
Printed circuit using laser and iron printing
Construction of the circuit with Purity spray
Circuit making with laser printing and laminator machine
Printed circuit production with laminate and UV
Circuit making with CNC
The most common manufacturing method for beginners is laser and iron printing, which is both easy and does not require many facilities. This method is often used to teach students and is not suitable for mass production. Anti-acid and letterpress magic methods are also very basic and are only useful for getting to know the technique and tools, and they are used in educational circuit kits because they are not very accurate. It can even be said that the positive spray method is one of the basic methods that are suggested to students and are more accurate than the previous methods.
In more professional printed circuit boards, laminate and UV are used, or mechanical and laser CNCs are used because it is both more accurate and more cost-effective in large-scale and high-volume productions.
As mentioned, different methods are used to make the printed circuit board, and you can consider the difficulty or ease of each of these methods, the available facilities, and the level of expectation from the quality of the resulting printed circuit board. Choose one of them.
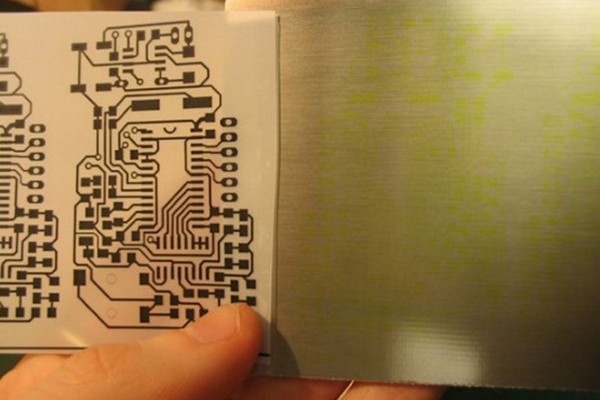
Making a printed circuit board
Familiarity with different methods of making printed circuit board
In this section of the Arya Madar
Arjomand website, we are going to introduce some methods of making a printed circuit board.
• Using laser and iron printing
• Using letter trust method
• By using CNC machine
• By using anti-acid magic
• Using lamination method and UV rays
• Using laser printing and heating device
• By using positive spray 20
Making a printed circuit board with anti-acid ink
This simple method is usually used by novices and at the beginner level, and the resulting board will not be very clean and accurate. In this method, anti-acid ink and printed circuit acid are needed and it takes a lot of time. In addition, the quality of the resulting printed circuit board can vary depending on the materials used. This method is not considered to be a suitable option for the production of boards at the medium and mass level. We will explain the steps of making a printed circuit board with this method.
1- First, clean the copper fiber with the help of a soft sandpaper or in any other way and make sure that there is no layer of fat or dirt on the copper.
2- Then draw all the required lines on the copper fiber with the help of a colorful anti-acid marker that is special for this task. Because there is a possibility of losing the magic color if it is of poor quality, in water and acid, after designing and spending a lot of effort.
3- Remember to avoid contact with the copper fiber due to its oiliness, because it can cause problems during the acidification stage.
4- You can use the stencil to create realistic sizes for parts such as ICs whose bases are approximately one-tenth of an inch apart, and by placing it on the copper, trace around it with a special marker that is sharp. draw With this method, you will be able to implement your entire design on fiber.
5- After completing the printed circuit board design, you can remove the excess parts of copper by placing the fiber in the acid.
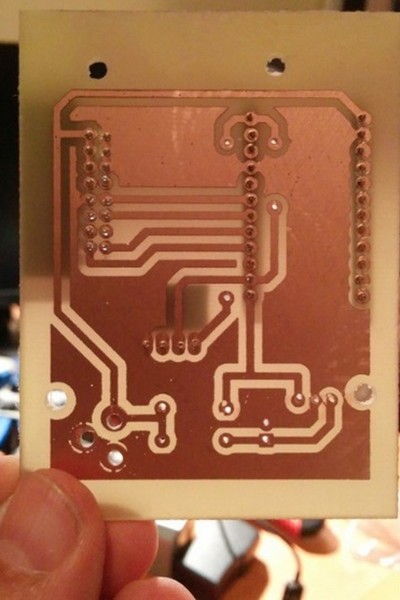
Making a printed circuit board with anti-acid ink
Making a printed circuit board using Letraset
This method, like the previous method of making a printed circuit board, is mostly used by beginners and the result will not be very accurate and clean. This method requires materials such as printing circuit acid and
Letraset.
Letraset means the same letters as the letters, except that dots and circular lines have replaced the letters on it. First, prepare a few point and line letter trusts based on the type of circuit and your diagnosis. In order not to face a problem when returning it to the copper fiber, be sure to use fresh
Letraset.
In the rest of this section, we are going to introduce the steps of making a printed circuit board in this way:
1- First, in order to remove any grease and dirt on the copper, you must completely clean the copper fiber with a soft sandpaper or any other method.
2- After that, proceed to draw the required lines with
Letraset on copper. You can reverse the dots and lines on copper with the help of a pen or other similar device. Don't forget to avoid touching the copper in order to prevent the copper from becoming greasy and not to disturb the acid step.
3- In the end, make sure that the points and lines on the copper are completely stuck, and if any of them are not stuck, stick them to the copper surface with the help of a hair dryer and heating. It is even possible to use an anti-acid marker to fill in the spots that are not well covered with letterpress.
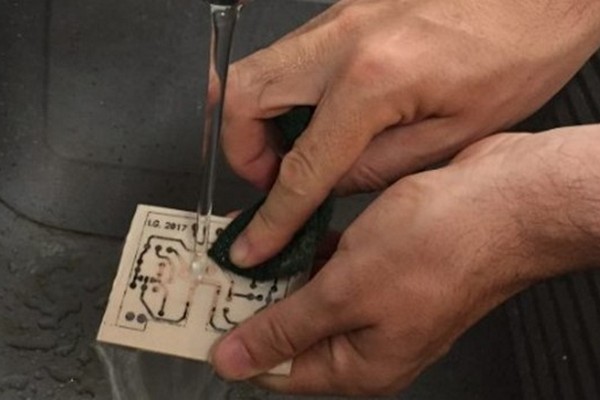
Making a printed circuit board using Letraset
4- In the next step and after completing the circuit, put it in acid to remove the excess parts of copper.
The method of making a printed circuit using laser and iron printing
In this method of making printed circuit board, materials such as suitable glossy paper, laser printer, as well as printed circuit acid and iron are used.
Making a printed circuit board with the help of this method is as follows:
1- Although instead of toner in the printer Liquid ink is used in inkjet printers, but the powder in the laser print cartridge or the toner is made of plastic, and this printer prints by sprinkling the powder on the paper and registering the toner with the help of heat from the laser. Gives. During printing, the toner will be transferred to the paper in powder form after leaving the cartridge. Since copper fibers are hard, you will not be able to use the printer directly to create lines and other marks on the printed circuit board. So you have to transfer the toner from the printer to the copper fiber indirectly.
A simple solution to solve this problem of making a printed circuit board is to first print the circuit with a resolution of 600 on a paper like glossy paper on which the toner is gently placed, and then heat the toner. Go through the iron a second time to melt it and finally transfer it to the copper fiber. (Since there is a possibility of losing this printed sheet in the later stages of the work, so try to place this printed circuit diagram on one or two A4 pages and use them as a backup).
Description of continued work:
The type of paper used is very important and it is better to be glossy in order not to absorb toner. In addition, it is possible to easily separate the toner from the surface of the paper and transfer it to the copper fiber by heating; It is also recommended to use completely white glossy paper so that you don't face any problems during ironing.
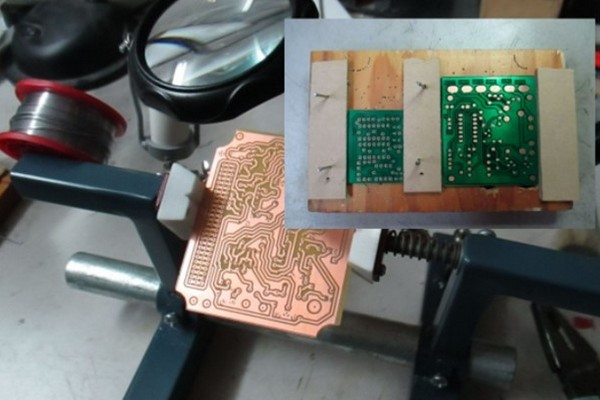
Using laser and iron printing, another method of making a printed circuit board
In addition, make sure that the design is printed as a mirror, because the default mode of most software when printing is on the option option. Another important point before transferring the image of the circuit is to completely clean the surface of the copper fiber with the help of dishwashing liquid, warm water and washing powder. Of course, to remove dirt on the fiber surface, you can go for fine sandpaper approximately 360. If the surface becomes dark after doing this, using a little lemon juice for cleaning seems like a good option and dry it at the end of the work. Remember not to touch the copper fiber after cleaning it so that you don't face a problem during acid work due to greasy fiber.
Board ironing step in laser printing and ironing method
2- After the work surface is completely cleaned and polished, it will be time to place the glossy paper on which the circuit is printed upside down on the copper fiber. For this purpose, iron it with a high temperature until the paper takes on a slightly dark color and sticks to the fiber. Note that at this stage, the heat of the iron must reach all points uniformly, therefore, be sure to do this continuously; Also, be careful that excessive ironing can cause the powder to spread and lead to the loss of the quality of the circuit. It can be said that considering about 10 minutes of ironing with high heat is enough to print a normal circuit. Of course, you will know the exact time by repeating the circuit print several times.
One of the signs of correct ironing that can be mentioned is a slight darkening of the color of the glossy paper attached to the fiber, as well as the appearance of the printed circuit design in a faint form from the side of the glossy paper. At this time, the temperature of the copper fiber is very high, so be careful with your hands when handling it.
3- In the next step, place the copper fiber in cold water, when the paper is pulpy and completely wet. Then by removing it from the water, separate the pieces of paper on it. At this stage, the complete and accurate transmission of the circuit design is done on the copper fiber.
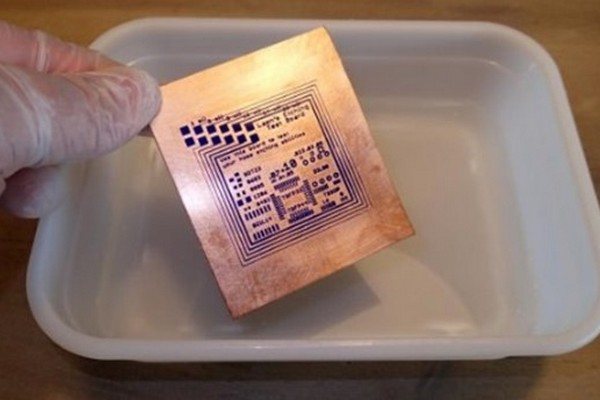
4- Removing the extra copper sections from the printed circuit board will be the next step of this method. Usually, an acid called chloridopheric, which is known as printed circuit acid in the market, is used to remove the copper parts without insulating coating. Perchloridopheric is available in the market in two forms, powder and crystal, and to use this acid, you need to add some of it to hot water so that the resulting solution becomes colored tea. When working with this acid, you should only use non-metallic containers such as glass and plastic containers.
Then, after preparing the acid solution, put the printed circuit fiber in it and start shaking it slowly. Removal of excess copper parts is done after a short period of time, which you should continue until it is completely gone. If the fiber is placed in the acid in an inclined manner, the effect of the acid will increase, and in such a case, be careful that the fiber stays in the acid for 5-10 minutes. Because the acid enters the parts under the print and will cause the design to fail.
5- In the next step, after removing the copper fiber from the acidic solution, wash it with cold water and remove the remaining toners on the fiber with the help of a dishwashing wire.
Making a printed circuit board with the help of laser printing and heating device
This method is very similar to the method of using laser printing and iron in making a printed circuit board (
PCB), and the only difference is that a heating device or card press is used instead of an iron.
Using positive spray 20
The positive spray method is suitable for student works. Positive spray 20, caustic soda (sodium hydroxide) and transparent talc or film are the materials needed to perform this method of making a printed circuit board. First prepare a positive spray 20. Note that if there is any spray left, Its tendency to be corrupt is high and it will not have the necessary sensitivity to light. To prepare caustic soda, you can go to a medical equipment store and buy it at a relatively cheap price.
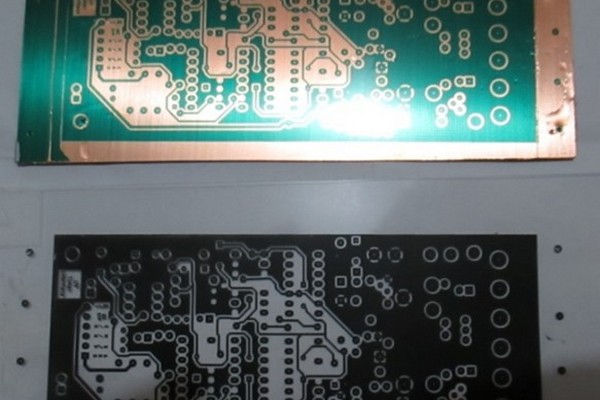
Making a printed circuit board with the help of laser printing and heating device
In the continuation of this section of the Arya Madar Arjamand website, we will describe the method of making a printed circuit board with this method.
1- First, in order to implement the design of the printed circuit board, prepare several sheets of transparencies that can be printed with laser printing. The color of the points and the path that should have copper according to the design is black and other points should be empty. Try to take two printed copies of your design and place them on top of each other to prevent light from passing through the printed areas.
2- Then, use a soft sandpaper to remove any grease and dirt on the copper fiber.
3- At this stage of making the printed circuit board, after the fiber is completely dry and clean, the copper surface is uniformly and Cover with regular movements. Of course, do this in a place away from wind and dust and in a dark place. If the fiber is completely covered with one spray, there is no need to repeat it again.
4- After that, let the copper fiber stay in a dark place for 12-24 hours to dry or you can do it by heating. If you have a fiber dryer, you can go for it. But otherwise, you should heat it gently to 70 degrees on an oven and in a metal container. A suitable container for doing this can be a large pot, in order to avoid direct heating of the fiber, it is a good idea to put some pieces of metal on the bottom of it. After 10-15 minutes the fiber will dry completely. One of the important points in this method is that all steps must be performed in a dark place.
5- Now by preparing another large container, put two to three ordinary lamps or a small gas or moonlight lamp according to the size of the design inside it. Then by placing a glass on the container, place the film or printed design on it.
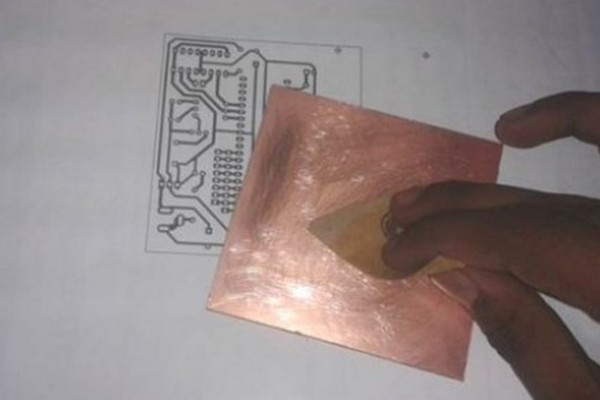
printed circuit board
6- After that, put the fiber so that the painted copper surface is down and on the printed design. Use a weight or another glass to weigh the fiber so that the fiber adheres to the design with high pressure during exposure. A dark place is needed to perform all these steps. Now, by turning on the moonlight or lamp, light it for 20-30 minutes, and of course, this time depends on the intensity of the light and, most importantly, the quality of the spray you use. So, if the spray is fresh, this time can be less than this amount. Because in these conditions, you will see a faster reaction from the fiber exposed to light.
7- Now dissolve caustic soda with water in a container. Then pour enough water in the container to cover one centimeter of the fiber and add approximately 10-20 grams of soda to it. If you use more than this amount of profit, it is possible that it will eat all the positive color. Now stir it to completely dissolve the soda in the water.
8- At this stage, put the copper fiber in the soda solution in an almost dark place and start shaking the solution very slowly for about 30-60 seconds. At this stage, you can dip some cotton in the caustic soda solution and gently rub it on the board. After a short time, you will see the voids slowly dissolve in the solution. Now quickly remove the fiber from the solution and wash it with water. Next, it is necessary to drop it into Perchloridopheric acid solution.
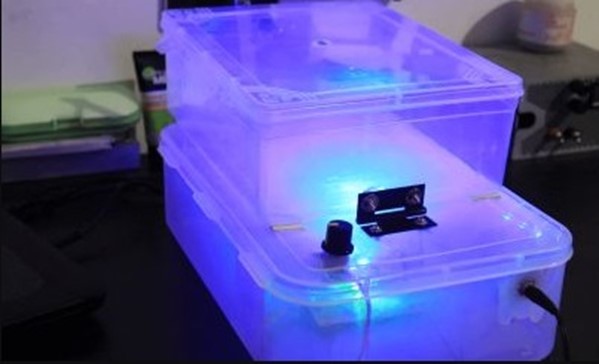
The method of making a printed circuit board
Making a printed circuit board with the help of laminate and UV rays
This method is suitable for very professional and precise work and is generally used in printed circuit board factories. In this method, the printed design of the negative circuit or the transparent and laminate based on the desired cross section and also the acid of the printed circuit are needed.
In relation to laminate, we should say that it is a light-sensitive plastic sheet with a small thickness and green or blue color, which in fact, a light-sensitive chemical substance is used between two plastic sheets. The plastic cover on one side is elastic and soft, and the cover on the other side makes a sound when separated and has a thin sheet. We will witness the color change of the laminate with intense light radiation in a short period of time, which also changes its chemical properties. The printed circuit prepared with the help of this technique is very accurate and clean and will not be different from the commercial samples of PCBs.
Description of the procedure:
1- First of all, you need to prepare a negative print of your design. First, draw the printed circuit diagram in a graphic program such as Photoshop, and then by comparing it, you should create your negative circuit diagram. Do not forget that the printed circuit map must be negative, that is, the place of the copper lines on it should be considered empty and the other places of the circuit should be black.
2- In the next step, try to remove any fat on the copper fiber with the help of soft sandpaper or washing it.3- Laying laminate on copper fiber can be considered the most important part of this method. After removing the softer layer of laminate halfway, place it on the fiber and proceed to glue the other side of the laminate to the fiber as you are removing the underside. Be careful not to create air bubbles under the laminate. If this happens, you should remove the air bubbles with a needle after gluing the laminate.
4- Now, in order to firmly stick the laminate on the fiber, run your hand over it for 5-10 minutes. To do this, in the industry, a heating device or card press with low heat is used. Ironing can also be a suitable option, but a wet cloth should be placed between the fiber and the iron and the iron should be set to a low level.
5- After finishing the work of making the printed circuit board, cut the extra laminates with a razor by reversing the fiber.
Using the UV device at this stage of making the printed circuit board
6- Then the laminate is exposed with the help of a UV device, which usually takes less than 1 minute. For this purpose, put the negative design on the device and then, by placing the fiber on which the laminate is placed, perform the exposure process. Do this for 1 minute.
7- Now, by removing the thin sheet on the laminate under soft light, prevent the unseen parts of the laminate from appearing.
8- At this stage, the emergence of the fiber is done. By doing this, the parts of the fiber that cannot be seen are separated. For emergence, you need to combine a tablespoon of emergence powder, which is baking soda or sodium bicarbonate, with some water. In other words, pour half a centimeter of water into a 20 x 10 cm container. Now put the fiber in it.
9- After 5-10 minutes, gently pull your hand on the fiber to separate the non-exposed laminates and finally wash the fiber under water.
10- Now it's time to acidify and remove coppers from the part of the printed circuit board iran that is not exposed to light. Don't forget that the unexposed copper parts are completely dissolved in the acid and are clearly visible. But other parts under the blue laminates will not be soluble in acid. For acidification, mix a ratio of 1 to 2 high chloridopheric acid in boiling water. Use a non-metallic container for this. Avoid pouring acid into water to prevent it from splashing in the eyes, and on the contrary, pour water slowly over the acid. Now by placing the fiber in the container, shake the container for 5-10 minutes to prepare the printed circuit board.
The step of removing the laminate from the board
11- Then use sandpaper or a razor to remove the laminate from the copper parts of the printed circuit board; But the best way to do this is to use caustic soda. Pour a third of a tablespoon of soda into a container and add half a centimeter of water to it. 1-3 minutes of time is needed to separate the excess laminates according to the soda concentration. Now your fiber is ready for drilling and then assembling parts on it.
Of course, the type of laminate plays a role in whether the printed circuit board design is positive or negative. In general, we must say that to use this method, you need UV insulation, printed circuit fiber sensitive to positive or negative light, distilled water and a transparent sheet. Maybe you can find a ready-made board, usually a black nylon sheet on it, and apply a special photosensitive spray on one side of the fiber, which has a copper coating. In the next step, try to print the printed circuit board design on a transparent sheet. Then cover the copper surface with a transparent sheet on which the printed circuit board is placed and align it. Now put both of them in the UV insulation device for 15-20 minutes. Also, use PHOTOREVELATOR to remove extra parts. Finally, clean it with distilled water and place it in the acid container.
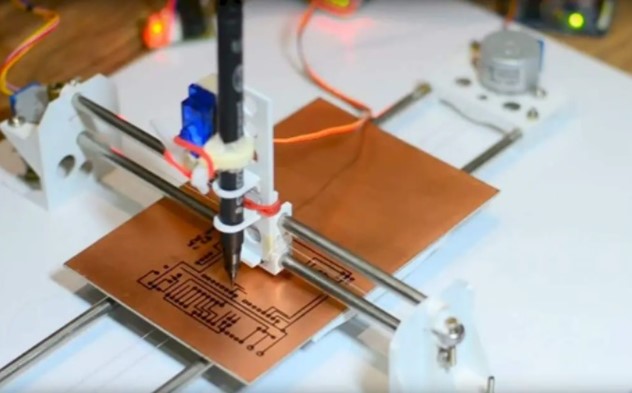
Making a printed circuit board with a CNC machine
Making a printed circuit board with a CNC machine
This method of making printed circuit board is suitable for producing printed circuit board with high circulation. This method does not require printing the design on copper fiber and also acid treatment. In this technique, after transferring the circuit PCB design to the computer of the CNC machine in the form of files with a special format, the machine will engrave the desired design on the copper fiber. Of course, the drilling process is done first and then engraving. Due to the expensiveness of this device, it will only be cost-effective to print a large number of printed circuit boards with it. It should be noted that the quality of the board obtained by this method is very high.
The printed circuit board is one of the most important electronic parts used in electrical devices and equipment. For the proper functioning of these devices, this very important part plays the main and most important role despite being small. It is on this basis that making a printed circuit is considered one of the most important steps in making all kinds of electronic devices. Some of the other names for these boards can be mentioned below:
• Electronic board
• Printed circuit
•PCB
• PCB board
The need for an expert in the manufacture of printed circuit boards
Some people think that making a printed circuit can be done by anyone with a little simple training. Maybe this issue is true in relation to circuit printing in very simple and common types, but it will definitely not always be the answer for all types of electrical devices. Especially, these parts have many applications and a special design is needed for each type of application. For this reason, the best option is to have all the work steps done by experienced professionals.
The experts active in this field know all the details of the work due to the design and manufacture of various types of printed circuits. First, they easily identify the best type of printed circuit board needed by a device. After accurately identifying the requirements of a device, they design and manufacture it with the best possible quality. But exactly what kind of electronic component is the printed circuit board? Does it fall?
High quality printed circuit board manufacturing
In order to make the printed circuit more clear, knowing the printed circuit board will be a great help in this field. Because by knowing the structure of these parts, what should be there to make these parts is also better defined.
These electronic parts consist of one or more layers. Dozens and sometimes even hundreds of parts such as resistors, capacitors, ICs and other parts are placed on this screen. The printed circuit board connects all these parts in the best possible way and in the least space. As mentioned, the printed circuit board can be designed in very simple types or in extremely complex models. All these printed circuits generally have the following two parts:
bottom board
This thin board has a diameter of approximately 1.6 mm. The material of this part is generally chosen from resin and fiberglass. This board is mostly available in green color in the market, but there are also orange, blue and yellow colors.
Thin layer of copper
This layer is electrically conductive due to its copper material. If the thin copper layer is used on one surface of the printed circuit, it is called a single-sided printed circuit. If the copper layer is used on both parts of the printed circuit board, it is called a double-sided printed circuit board. The copper is placed in the printed form on the bottom board. Any parts that are necessary to give proper functioning to electrical devices are soldered on this board. This electronic board connects all these parts.
Applications of printed circuit
The importance of making a printed circuit becomes more clear when its different types are seen in all electrical devices. In fact, today's modern devices will not work without these electronic parts. Some systems and devices that can only work with a printed circuit board include the following:
• Sound and music broadcasting systems
• Air conditioning systems
• Microwave device
• TV remote control device
• Lighting tools
• Electric heater chambers
• Robotic vacuum cleaners
• Digital watches
• Home alarm devices
• CD players
• Home theaters
• Handheld video games
• Electric toys with remote control
• Television
• Computer
• Cellular phone
• washing machine
• Iron
Essential tips for manual printed circuit construction
With all the explanations mentioned, people who are interested in making PCB manually without using modern equipment for any reason should keep the following points in mind so that they don't get into trouble:
Wear plastic gloves.
Place a newspaper or a suitable mat under your workplace so that your work floor is not damaged.
Dissolve 2 to 3 teaspoons of iron chloride in water.
Place the PCB in the etching solution (iron chloride solution, FeCl3) for approximately 30 minutes.
FeCl3 reacts with unmasked copper and removes unwanted copper from the PCB (this process is called etching).
Use the pliers to pull out the PCB and check if the entire uncoated area is etched. If it is not engraved, leave it in the solution for some time.
High quality printed circuit board manufacturing
Remember that only doing a basic job can result in a device with good performance. In addition, to have devices that work in the best possible way for a long time, you need to print the circuit in a basic way; Therefore, choosing a collection like Arya Madar Arjomand, which has a long successful history in this field, is considered the best option.
This Group, with its expert staff, can design and manufacture printed circuit boards from zero to one hundred. Because the knowledge and experience of the employees are such that they perform all the steps at the highest possible level. In general, this company advances from the procurement of all kinds of parts necessary for the work to the quality control according to the customer's opinion. With this work policy, customers get exactly what they want. In addition, this company has made all the work process easier for its customers by designing the printed circuit board online. In this way, the whole work is executed in a completely precise and calculated manner, as quickly as possible and with excellent quality.